HEULE's Gary Brown on Cross Hole Deburring
Swiss Precision Since 1961
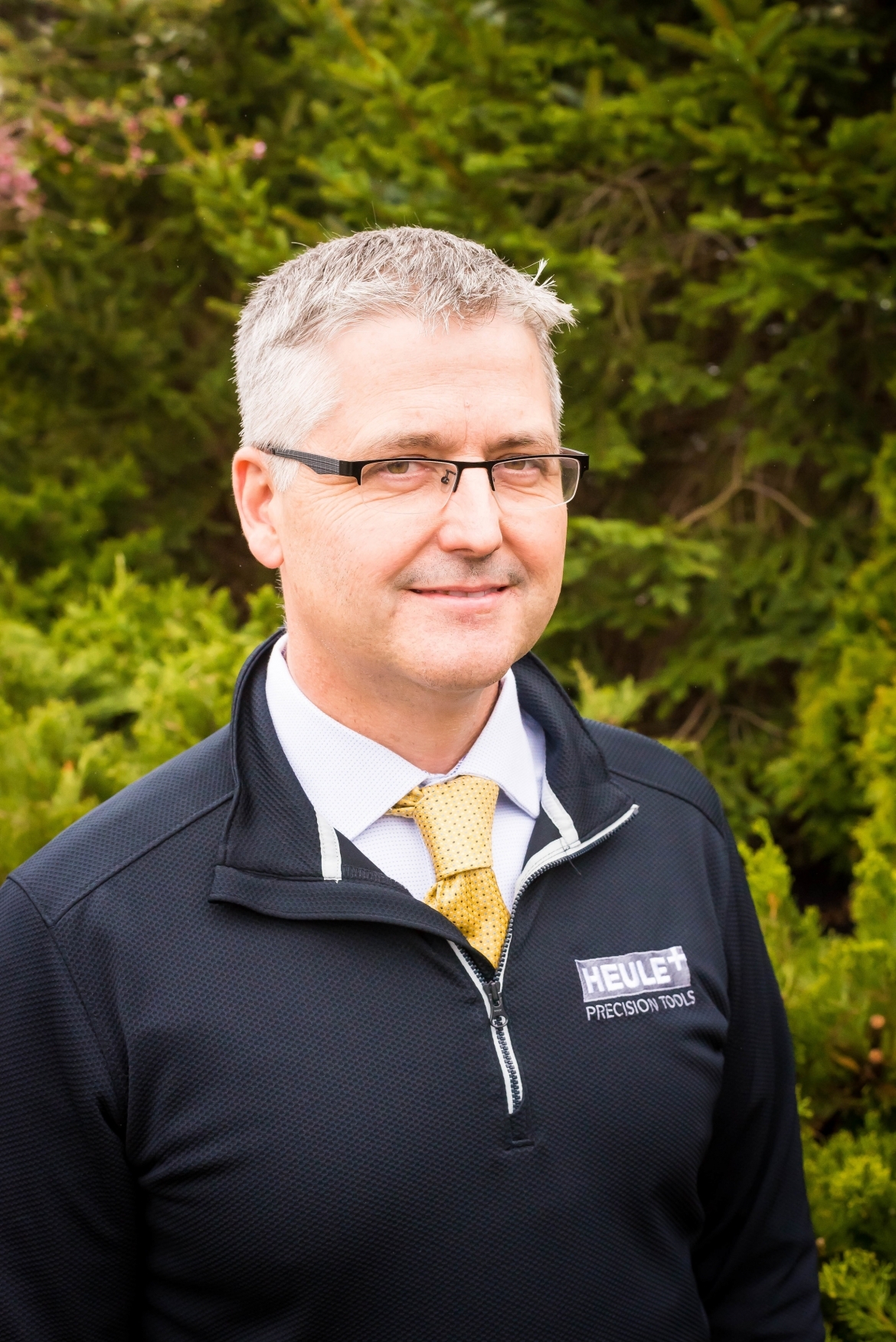
In his recent guest blog for Shop Metalworking Technology, deburring expert Gary Brown talks about the challenges and solutions involved with deburring cross holes.
Machinists and programmers alike know how demanding cross hole drilling can be, as it often exacerbates many of the difficulties inherent in metalworking.
Deburring is already a painstaking process, but when burrs are difficult to inspect and access, as is the case in cross hole intersections, traditional deburring methods are time consuming and inefficient.
Regardless of size, or whether the hole is threaded, angled or off-center, any time a hole is drilled into a part, it will create a burr: ragged edges, particles, protrusions or shavings not removed by the initial drill pass.
These imperfections can create off-spec parts or increase the likelihood of injuring a worker that handles machined parts or blanks. In many manufacturing applications, it is vital that through-holes are chamfered and absolutely free of metal burrs, as flawless fit and durability are the top priority when parts are assembled. When the intersecting parts move, the importance of fit increases exponentially, as any additional source of friction at the edge breaks will abrade the part, leading to premature failure. When the part is used in applications involving fluid or liquid, burrs in the pipe can slow down or obstruct the flow of the liquid.
The closer the bore gets to a 1:1 ratio, the more difficult and expensive the bore is to deburr. Intersecting bores result in elliptical-shaped bores where burrs build up in the areas where the bore dips. The burrs are difficult to see, and even more difficult to access–but all the more important to remove.